Store more in a smaller footprint.

Multiple Days
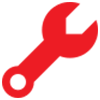
Intermediate
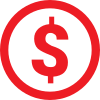
$501-1000
Introduction
There never seems to be enough storage space in garages, but rollout shelves and sliding bypass units can make more efficient use of the sidewalls of your garage.
Sliding Shelves Overview
Check this out!
This bypass door hardware is the key to smooth-gliding rollouts.
Let’s face it. No matter how big your garage is, there never seems to be enough room to store everything. But by making ultra-efficient use of the narrow area on the sidewall of your garage, this storage project can help.
The heart of the system is a series of double-sided rollout shelves that allow easy access to everything that can be stored in a narrow space. With these rollouts, you don’t have to store your paint cans, nails, screws and other stuff four layers deep and then shuffle everything around to find what you’re looking for. When the shelves are pulled out, everything is in full view and easily accessible. Plus, the garage looks neat and tidy when the shelves are pushed back in.
Don’t worry if you’ve also got some large items to store. The 16-ft.-long top shelf is 32 in. deep to hold big storage containers, and there’s a 3-ft.-wide section of 16-in.-deep shelves for medium-size items. The storage unit is 16 ft. long, 84 in. tall and 16 in. deep.
The cost of the materials for this project is about $800. If you want to save some money and don’t require as much narrow storage space, just reduce the number of rollout shelves. Each rollout, including hardware, costs about $75.
Expect to spend three or four days building this project. It’s not complicated or difficult, but there are a lot of parts to cut out and assemble. For the most part, we used standard carpentry tools, but we used a table saw to cut the particleboard and a biscuit joiner and pocket screw jig to assemble the rollouts and bypass unit. The latter tools are optional, though. You can cut parts with a circular saw, but it’ll take longer and won’t be as accurate. And you can substitute screws and glue for the biscuit joints. You can also nail through the face of the cabinets to secure the divider rather than use pocket screws.
The particleboard and framing lumber you’ll need are available from home centers and most lumberyards. The bypass door track and three-wheel rollers we used to support the shelves may be hard to find locally, but you can order them online at johnsonhardware.com. You can also buy the shelf standards and leg levelers online at wwhardware.com.
Sliding storage = More convenience, more space
The rollout shelves provide better access and make small stuff easier to find. They’re versatile, too. You can set the divider wherever you want to create different-depth shelves.
The bypass unit adds 50 percent more storage for long-handled tools and all sorts of items that take up too much wall space. You simply slide it to either side to access the stuff behind.
Tools Required
- Air compressor
- Air hose
- Biscuit joiner
- Brad nail gun
- Circular saw
- Cordless drill
- Countersink drill bit
- Framing square
- Hammer
- Jigsaw
- Level
- Miter saw
- Orbital sander
- Pocket hole jig
- Safety glasses
- Stepladder
- Stud finder
- Table saw
Project step-by-step (12)
Map it out on the wall
Mark the wall
Make a level line to indicate the bottom edge of the top shelf, and then mark the location of all four columns. Draw plumb lines to mark the edge of the 2×2 cleats.
Mark the location of the top shelf and columns on the wall before you start building (Photo 1). This allows you to check for obstructions and double-check the height of the columns. Start by deciding where the endpoints for the 16-ft. storage unit will be. If you have leeway, you could adjust the position so that the end columns land over wall studs, but it’s not necessary.
Next, use a level to see if the garage floor slopes. Measure 81 in. up from the highest point on the floor and mark the wall. Draw a 16-ft. level line across the wall from this point. We used a laser level to establish level reference points on each end of a 16-ft. line, and measured up from these points to mark the endpoint of the horizontal layout line. Then we snapped a chalk line between these points to indicate the bottom edge of the shelf and the top of the columns. You could also use a line level or step a 4-ft. level across the wall to mark the level line.
If your garage floor slopes more than 1-1/2 in. from one end of the unit to the other, you’ll have to build some of the columns a little taller. Check this out by measuring down from the level line at each end. Finally, using Figure B as a guide, carefully mark the location of the wall cleats that anchor each column, and draw plumb lines down from each mark (Photo 1). Now you’re ready to build the columns and wide shelf.
The 50 Best Storage Containers to Get Your House in Order
Figure A: Garage storage system
Figure A shows the construction and parts of the garage storage system. Modify the size to fit your space.
Figure B: Top shelf details
Align the frame and the column locations.
Assemble the columns and shelf
Assemble the columns
Wood glue creates a strong bond on particleboard and makes a strong assembly. Use brads to hold the parts together until the glue sets.
Install leg levelers
Garage floors tend to be damp and unlevel. Adjustable leg levelers on the bottom of each column keep the columns dry and adjust to sloping floors.
Install the columns
Slip the columns over cleats mounted to the wall. It’s easy to adjust the height and plumb the face of the column before screwing it to the cleat.
Attach the tracks to the shelf frame
To avoid working overhead later, screw the tracks to the shelf before you install it. Use the dimensions in Figure B to lay out the track locations.
How to Build Pull Out Under Sink Storage Trays for Your Kitchen
Set the frame on the columns
Align the ends of the shelf with the outside edges of the columns and screw it to the studs.
Cut out the parts according to the Cutting List (the Cutting List and a Materials List are available in pdf format in Additional Information below). Then build the columns. Photo 2 shows how to assemble the columns using wood glue and finish nails. Let the glue set. Then install the leg levelers (Photo 3). Mount the cleats on the wall at each of the column locations. Use toggle-type hollow wall anchors to anchor the cleats if there aren’t any studs to screw into. We used Toggler Snaptoggle anchors, which are easier and faster to install than standard toggle bolts.
Mount the columns by slipping them over the cleats and driving screws through the sides into the cleats (Photo 4). We had to notch the bottoms of the columns to fit around the protruding foundation block. If you have a similar situation and the block is more than 6 in. above the floor, make sure to either shorten the rollout shelves or make them narrower so they don’t run into the protruding foundation.
Adjust the leg levelers until the tops of the columns are even with the horizontal line. Then set a level against the front edge to make sure the column is plumb. You can slide narrow shims between the wall and the back edge of the column if necessary to plumb the column. When the column is plumb and the top is even with the level line, drive screws through the side and into the cleats. The next step is to build and install the horizontal shelf.
Screw 2x4s together to make the top shelf using Figure B as a guide. It’s easier to attach the aluminum tracks to the shelf before you lift it onto the columns (Photo 5). Use Figure B as a guide for marking the track locations. Cut the tracks to 32 in. with a hacksaw. Then drill holes for the mounting screws. Attach the tracks with 2-in. pan head or washer head screws.
Mark the stud locations on the wall. Then lift the shelf onto the columns and screw it to the studs with 4-in. structural screws or lag screws (Photo 6). Screw 3/4-in. particleboard to the top of the shelf frame. Check with a framing square to make sure the columns are at a right angle to the wall before you toe-screw the front of the columns to the shelf frame.
Build the rollout shelves and bypass
Cut biscuit slots in the rollout parts
Cut three biscuit slots on the face of the sides and matching slots on the ends of the top and bottom. The right angle support allows us to use the workbench top to support the biscuit joiner.
Assemble the rollouts
Join the sides to the top and bottom of the rollouts with biscuits and wood glue. Clamp the parts together until the glue sets.
Install the rollout divider
Use spacers to support the divider while you screw or nail it to the sides of the shelf. Vary the size of the spacers to create different-width shelves.
Mount the rollers
Adjustable rollers allow you to fine-tune the rollout shelves after they’re installed. Each pair of rollers is rated for 125 lbs., for a total weight limit of 250 lbs. per rollout.
Photo 7 shows how we used a biscuit joiner to slot the sides of the rollouts. For more information on this “bench reference” biscuit joining method, see “Building cabinets with biscuit joints.” Mark the orientation of the parts by putting a piece of masking tape on the side facing you. When you assemble the parts, face the tape to the inside of the rollout. Glue and clamp the sides to the top and bottom (Photo 8). Glue a second layer of particleboard to the top for extra strength and to allow for the 1-1/2-in. roller mounting screws. Photo 9 shows how to support the center divider with spacers while you attach it with pocket screws. If you don’t have a pocket screw jig, just drive finish nails through the front and back of the rollout to secure the divider. You can adjust the position of the divider to accommodate your items. We moved one off-center to allow for 7-in.-deep shelves and built another unit with full-depth shelves. Use the same method to build the large bypass unit.
Finish the rollouts by attaching the roller mounting brackets (Photo 10) and the metal shelf standards. Draw lines 1 in. from the edge as guides for the brackets. Drill pilot holes and attach the brackets with 1-1/2-in. screws. Position the shelf standards about 3/8 in. from the front and back of the cabinet. We used 1/2-in. No. 4 flat head screws to attach the standards, but you can also use the small nails usually included.
Mount the rollouts and bypass
Install the rollouts on the tracks
Slide the rollers into the tracks to hang the rollout shelf. It’s easy if you pile up some scraps to support the heavy rollout while you align the rollers.
We used different techniques to hang the rollout shelves and the bypass unit. For the rollouts, it’s simpler to connect the rollers to the top of the shelf first and then slide the wheels into the tracks (Photo 11). For the bypass unit, install the rollers in the track before you mount it, and then hang the bypass by sliding the rollers into the mounting brackets.
To prevent the rollers on the rollout shelves from bumping into the face trim, screw 1-1/2-in.-square blocks of particleboard to the outside end of each of the rollout shelf tracks. After all the rollouts are hung, adjust the rollers until the spaces between rollouts are even and the faces are flush when they’re pushed in. Use the small wrench included with the rollers to turn the adjusting bolt located just below the rollers.
How to Organize: Garage Storage Projects
Finish up with trim boards
Add the finishing touches
Finish up by nailing strips of particleboard over the front edge of the top shelf and the face of the columns. You can stain or paint the particleboard or just brush a coat or two of polyurethane over it.
Complete the project by nailing strips of particleboard trim to the face of the columns and to the face of the top shelf (Photo 12). Two 8-ft. trim pieces will just cover the front edge. Then overlap the side pieces at each end. We also screwed sheets of particleboard to the wall behind the bypass unit to provide an attachment surface for hooks and other hanging hardware. We stained the columns and trim black, and the face of the rollouts and the bypass unit with Cabot Early American stain. When the stain was dry, we brushed two coats of Minwax Oil-Modified Polyurethane finish over the whole works to provide a little sheen and extra protection. If you plan to stain and finish the storage unit, consider doing it before you assemble the parts. It’ll save you a lot of time and effort.
75 Best-Ever Storage Tips for Your Home
Project PDF Files
Click the links below to download the construction drawings, materials list and cutting list for this project.
Cutting and Materials Lists and Construction drawings